In der Industrie gibt es aufgrund des globalen Wettbewerbs mit nationaler und internationaler Konkurrenz einen hohen Kosten- und Zeitdruck in den Bereichen Entwicklung und Produktion. In Branchen wie der Automobilindustrie sind effiziente mechanische Fügeverfahren wie das Clinchen zur Verbindung von Bauteilen fest etabliert. Verwendung finden diese insbesondere beim Fügen von Multimaterialstrukturen und Anbauteilen sowie dem Verbinden von Anbauteilen mit der Primärstruktur, wie es z.B. im Karosseriebau der Fall ist.
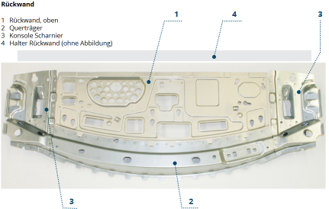
Problemstellung
Zur Verbindung mit anderen (An-)Bauteilen stehen Unternehmen im Entwicklungsprozess eine Vielzahl an Kombinationsmöglichkeiten aus Fügeverfahren und Fügeparametern zur Verfügung. Die Einflüsse auf einen erfolgreichen Setzprozess sind umfangreich dokumentiert. Allerdings fehlen wichtige Informationen über die notwendige Anzahl an Fügepunkten, deren Ausprägung, die exakte Fügestelle sowie die Wechselwirkung zwischen den Fügepunkten, um eine optimalen Verbindungsfestigkeit im Fügepunktlayout herzustellen. Aufgrund dessen werden Bauteile aktuell unnötig „überfügt“ und es wird nicht immer das kostengünstigste Verfahren ausgewählt, um die Verbindungsfestigkeit sicherzustellen.
Zielstellung und Lösungsweg
Das Ziel des Forschungsvorhabens ist die ermüdungsgerecht optimierte Auslegung des Fügepunktlayouts für umformtechnisch gefügte Bauteile. Dazu wird zunächst der Clinchprozess numerisch analysiert und Hilfsroutinen zur Ergebnisverarbeitung geschrieben. Anschließend werden Ein- und Mehrpunktproben bei verschiedenen Ermüdungslastfällen nach einem statistischen Versuchsplan sowohl im Experiment als auch in der Simulation, unter Verwendung des Örtlichen Konzeptes, untersucht. Die Informationen zu den Fügepunkten sowie den Ergebnissen werden in einem „Fügekatalog“ zusammengefasst. Dieser wird im Anschluss als Metamodell in einer Optimierungsroutine verwendet, um die Ermüdungsfestigkeit einer praxisnahen Bauteilgeometrie zu optimieren. Abschließend wird ein erfahrungsbasiertes Fügepunktlayout dem optimierten Fügepunktlayout unter Ermüdungsbelastung gegenübergestellt, um die Güte der Optimierung zu bewerten.
Nutzen
Insbesondere KMU als Zulieferer der OEMs der Automobilbranche werden mit der Optimierungsroutine im ersten Schritt befähigt, das Clinchen im Fertigungsprozess effizienter und gezielter einzusetzen und die geeignetste Kombinationsmöglichkeit aus Fügeparametern, Fügepunktanzahl und Fügestellen auszuwählen. Durch die Modularität der Optimierungsroutine können die Ergebnisse auf verschiedenen Ebenen verwendet werden: Von der reinen Verwendung der breiten Informationen aus dem Fügekatalog, über die Verwendung der zugrunde liegenden Metamodelle über eine GUI zur Optimierung mit anderen Randbedingungen, bis hin zur Anpassung der Optimierungsroutine auf eigene Anwendungsfälle mit z.B. anderen Fügeverfahren und Werkstoffen.