Auf einem volatilen Markt mit steigender Nachfrage nach Qualität und Flexibilität stehen Unternehmen zunehmend unter großem Druck. Mit steigenden Qualitätsansprüchen der Kunden bei gleichzeitiger zunehmender Nachfrage müssen Unternehmen sowohl flexibel agieren können als auch Ihre Prozesse stabil halten. Die steigende Nachfrage nach Transparenz in der Lieferkette der OEMs treibt darüber hinaus Zulieferunternehmen steigend in Zugzwang. Für Tiefziehteile, die kundenseitig höchsten qualitativen Anforderungen unterliegen und gleichzeitig komplexe Strukturen aufweisen, steigt die Herausforderung mit jedem Fertigungsschritt signifikant. Hierfür wird in dem Projekt ein Produktionssystem geschaffen, was dem produzierenden Unternehmen einen ganzheitlichen Ansatz zur Qualitätssicherung zur Verfügung stellen sowie die Transparenz über alle Fertigungsstufen gewährleisten soll.
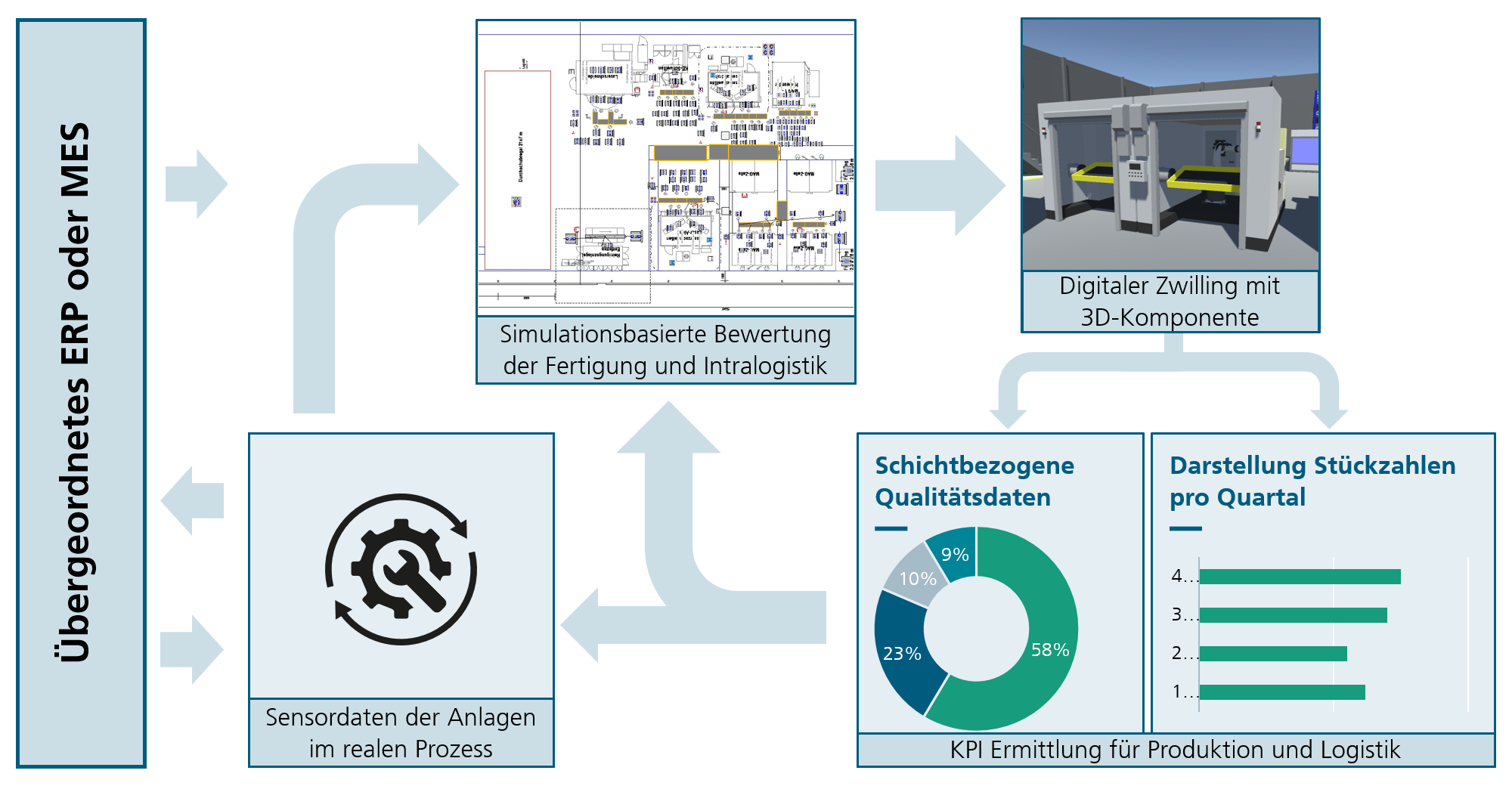
Problemstellung
Jede Art von Bearbeitung von Bauteilen führt zu einem Einbringen von Kräften in diese. Da aufgrund der verschiedener Einflussfaktoren (Qualität des Materials, Zustand der Werkzeuge, Einbringung von Kühlmittel, u. a.) Produkte zu einer Abweichung von Normwerten neigen, die zuvor in der Konstruktion als ideal ausgelegt wurden, bedarf es gewisse Toleranzgrenzen, in denen sich bewegt werden darf. Bei komplexen Strukturbauteilen, die eine geringe Fehlertoleranz und eine hohe Positioniergenauigkeit sowie Lagegenauigkeiten von Bohrungen aufweisen, führen solche Einbringungen von Kräften und Verzügen durch Wärmeeintrag oftmals zu höheren Ausschuss- und Nacharbeitsquoten. Diese Quoten und zusätzlichen Zeiten sind bei hohen beauftragten Stückzahlen weitestgehend zu minimieren, um weiterhin wirtschaftlich und weltweit marktfähig zu bleiben.
Lösungsweg
Durch die Verknüpfung von intelligenten Logistiksystemen, die eine Vertaktung zwischen den einzelnen Bearbeitungsstationen ermöglichen, mit einer durchdachten Messstrategie sowie der Einbringung von Automatisierungsansätzen, ist es möglich die Durchlaufzeiten innerhalb der Produktion solcher Bauteile bei gleichzeitiger Einhaltung vorgegebener enger Toleranzgrenzen zu minimieren. Der Ansatz der Umsetzung eines digitalen Abbildes der Produktions- und Logistikprozesse führt darüber hinaus zu einem ganzheitlich transparenten Produktionsnetzwerk innerhalb des Unternehmensstandortes. Damit ist es möglich, die Prozessparameter bauteilbezogen aufzuzeichnen und für den Kunden bereitzustellen. Fehler und Störungen der Anlagen können frühzeitig erkannt und Maßnahmen durch den sogenannten Topfloor auf der Shopfloor Ebene gestartet werden. Durch den Einsatz von Simulationswerkzeugen können darüber hinaus frühzeitig die Engpässe der Produktion ermittelt und planerisch gut ausgelegt werden.
Nutzen
Der Einsatz cyberphysischer Produktionssysteme ermöglicht dem Kunden eine Einsicht in die Prozesse der Produktion, ohne dabei direkt in das System eingreifen zu müssen. Die Qualität soll durch die hier beschriebenen Methoden und Werkzeuge kontinuierlich stabil bleiben und für den Kunden des Projektpartners Vertrauen schaffen. Zusätzlich soll langfristig eine Wirtschaftlichkeit der Produktion der komplexen Strukturbauteile und eine zunehmende Marktpräsenz forciert werden, die trotz steigender Nachfrage für den Projektpartner realisierbar bleibt. Die Stärkung der in MV befindlichen Unternehmen schafft darüber hinaus für den Standort Laage als auch für die gesamte Region interessante neue Aufgaben und attraktive Arbeitsplätze.