Im maritimen Bereich ist die Digitalisierung der Prozesse ein wichtiger Baustein für die Zukunftsfähigkeit der Werften. Die Forderungen des Weltmarktes hin zu immer kürzeren Lieferzeiten von Spezialschiffen zwingen sie zur Steigerung der Produktivität und Prozessoptimierung in allen Fertigungsebenen.
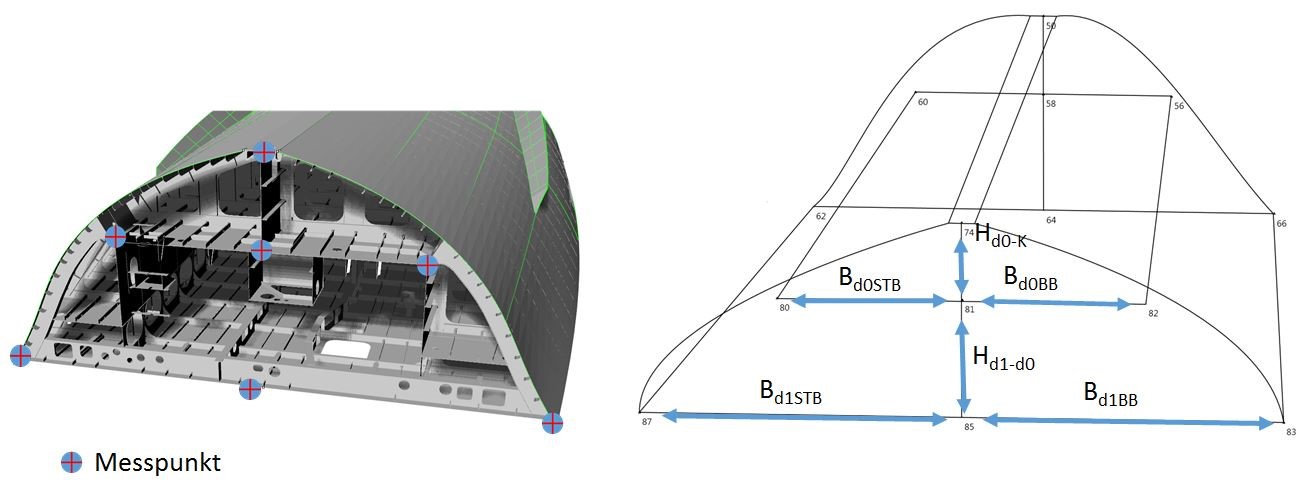
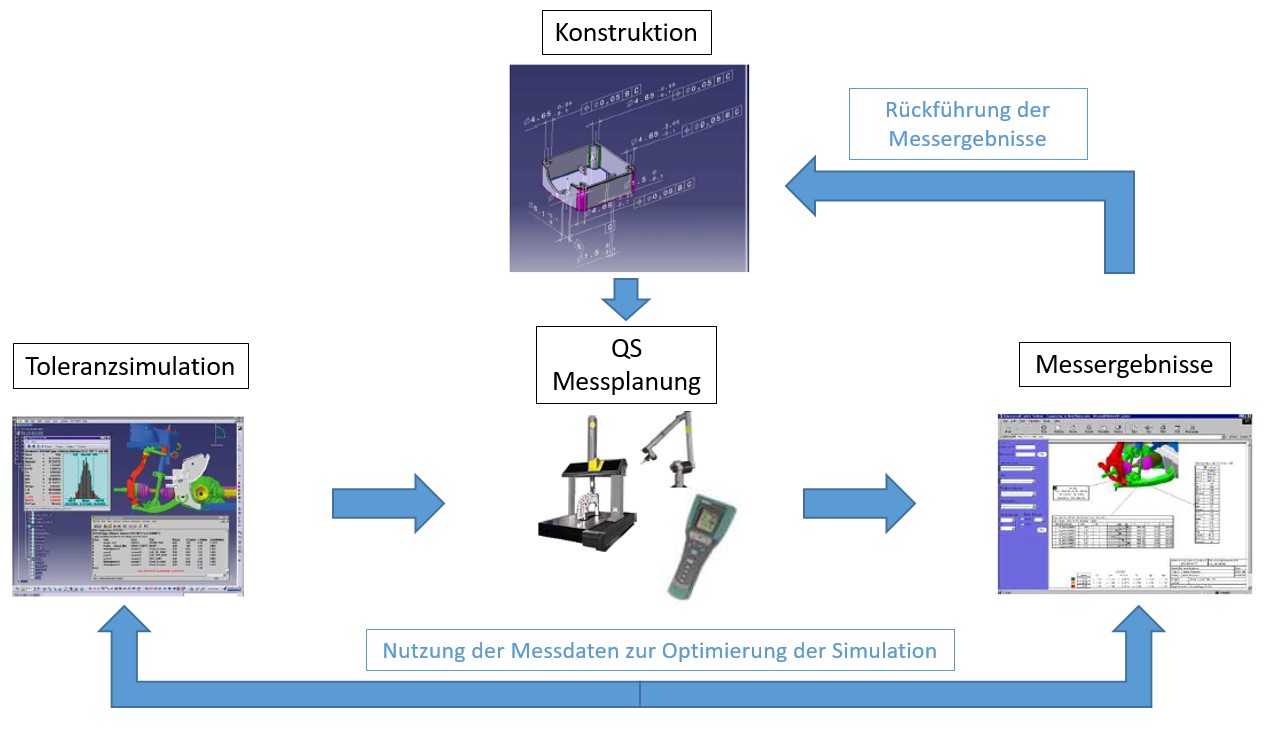
Problemstellung
Im Bereich des komplexen Montageprozesses von Volumenstrukturen im Schiffbau fehlt es derzeit an Verfahren und Methoden zur frühzeitigen Erkennung und Bewertung von geometrischen Abweichungen sowie der zielgerichteten Optimierung der Montageprozesse. Sektionen und Blöcke werden derzeit erst nach Abschluss des gesamten Montageprozesses punktuell geprüft. Fertigungsbegleitend werden nur stichprobenartig, nicht dokumentierte Maße kontrolliert. Ursache dafür sind der enorme Zeitaufwand, um umfangreichere Messungen durchzuführen, sowie das Fehlen von definierten Prüfmerkmalen und belastbaren Toleranzgrenzen für einzelne Fertigungsschritte. Signifikante Abweichungen, die einen hohen Anteil an Nacharbeiten erzeugen, werden dadurch zu spät erkannt.
Zielstellung und Lösungsweg
Ziel des Forschungsvorhabens DiGoCheck ist es, durch den effektiven Einsatz moderner Technologien den Prozess der geometrischen Qualitätssicherung im Montageprozess großvolumiger Strukturen zu digitalisieren. Anhand der durchgängigen digitalen Dokumentation der Produktionsprozesse können zu jedem Fertigungszeitpunkt Prozess-, Produkt- und Qualitätsdaten abgefragt und so der komplexe Montageprozess möglichst frühzeitig virtuell abgebildet, bewertet und zielgerichtet optimiert werden. Zur Erreichung der Zielstellung stützt sich das Verbundvorhaben auf die Entwicklung einer Prozesskette mit digitalem Informationsfluss zur Integration moderner Mess-, Auswerte- und Visualisierungstechnologien, bei der auch die Analyse von Toleranzen in der Fertigung von Volumenstrukturen berücksichtigt wird. Das Fraunhofer Institut für Großstrukturen forscht dabei an neuen Mess- und Auswertestrategien zur schnellen und umfassenden geometrischen Vermessung von Volumenstrukturen und Sektionen durch 3D-Laserscanning und der softwareseitigen Bereitstellung umfangreicher geometrischer Informationen als Teil der automatisierten Datenauswertung. Dadurch lassen sich Abweichungen und Prüfgrößen zügig digitalisieren, weiterverarbeiten und im Anschluss mittels AR-Technologie visuell aufbereiten und in die Fertigung zurückführen. (z. B. positionsgerechte Anzeige von Abweichungen).
Nutzen
Laserscanner bieten auf Grund der Messgeschwindigkeit und Messgenauigkeit das Potential für eine Onlineprozesskontrolle, wie sie bisher im Schiffskörperbau nicht möglich ist. Dazu muss der gesamte Prozess der geometrischen Qualitätssicherung angepasst und digitalisiert werden. Der wesentliche Fortschritt zur Steigerung der Produktivität und Wirtschaftlichkeit ergibt sich aus der automatischen Extraktion der geometrischen Daten, der Überarbeitung der Prozesskette zu einem digitalen Prozess mit gültigen belastbaren Qualitätsvorgaben für Volumenstrukturen und einer umfassenden Rückführung der Ergebnisse auf Planungs- und Fertigungsebene durch die Anwendung smarter Technologien aus dem AR-Bereich.